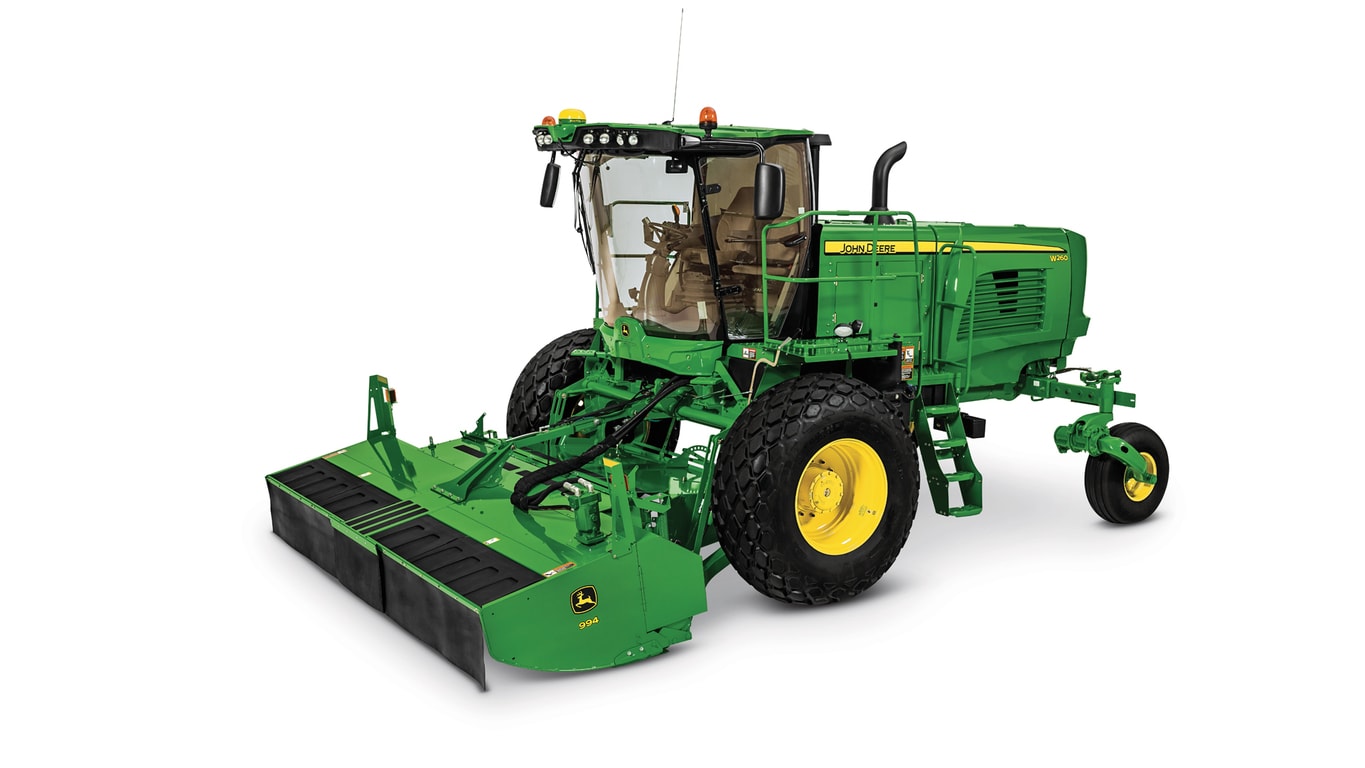
Key Features
- John Deere-designed rotary cutterbar
- Patented diagonally cut module
- Hydraulic cutterbar angle adjustment
- Adjustable impeller conditioning hood
Features

Large oval disks with free-swinging knives are used to cut the crop.
Knives are free-swinging to reduce damage if a solid object is struck.
-
Knife tip speed is variable and can be adjusted from the cab to improve cutting in light crop conditions
-
Knives are reversible to double useful life
-
Knives are removed and replaced at the front of cutterbar for convenience
- All cutting disks are the same size
- Disks are computer-designed for improved wear and cutting performance
- Cutting disks are made of high-strength, austempered steel
-
Austemper heat-treating process assures that the steel is thoroughly and evenly tempered for good wear characteristics
-
Wear caps
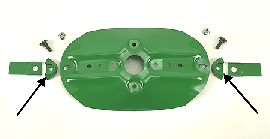
Wear caps are installed on each end of the cutting disks (except on the end disks where crop accelerators are used) to increase the wear life of the cutting disks and knife bolt nuts.
Wear caps are open on the end to prevent debris from packing in close to the nut, making hardware and knives easier to change.
They are made of austempered, heat-treated ductile steel.
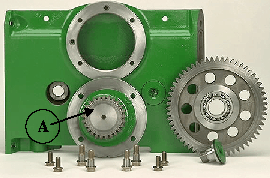
The John Deere-patented-design cutterbar is made from individual, diagonal-cut modules.
Serviceability is easy. Modules can be removed individually while leaving the cutterbar attached to the frame.
The modules are made of high-strength, nodular iron castings. Each module consists of two idler gears and one drive gear. The large-diameter idler gears transmit power from module to module. The idler gears turn at a relatively slow speed for added durability.
A smaller-diameter pinion drive gear is used only to power the cutting disk. Power is not transmitted from one cutting disk to another except through the large-diameter idler gears.
Modules are interchangeable. Disk rotation is determined by the position of the quill (A).
There is a rubber oil seal between each cutting module.
The 995 Rotary Platform features a single conditioning option: the impeller conditioner.
Impeller conditioner
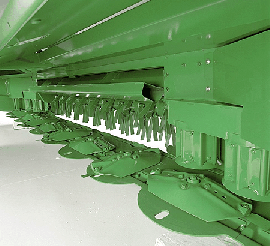
The impeller conditioner works well in a wide variety of crop types and conditions. With proper adjustment, the impeller conditioner delivers a wide range of performance expectations to meet every producer's needs.
How an impeller conditioner works:
1. As hay is cut by rotating knives, 72 V-shaped tines pick up the plants and carry them through the machine. The free-swinging design reduces damage to the conditioner if rocks or other solid objects are struck.
- Tines are evenly spaced along the full width of the rotor
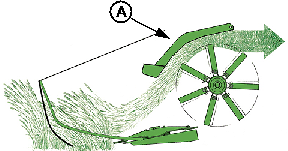
2. As the plant passes through, it rubs against the conditioning hood (A) and other plants. The rubbing action removes the waxy surface from the stem of the plant to allow faster evaporation of moisture.
3. The conditioner hood is adjustable to control the conditioning intensity. The wider the opening, the less aggressive the conditioning; this is used in legume-type crops. The smaller the opening, the more aggressive the conditioning; this is used more in grass hay.
4. The impeller has two speeds to match crop conditioning requirements:
- Simply interchange the drive sheaves
- High speed of 865 rpm for grass hay
- Low speed of 624 rpm for legumes
The impeller conditioner works well in legumes, especially alfalfa and most all-grass crops. Impeller conditioners are not recommended for cutting thick-stemmed or cane-type crops over 1.5-m (5-ft) tall.
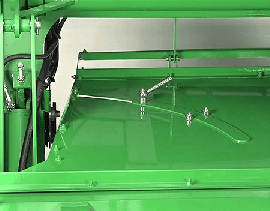
Forming shields are easily adjusted to control the material flow. This allows the operator to match the windrow width to the harvesting requirements.
The adjustable swathboard controls the angle at which the crop flow contacts the forming shield, providing additional control of windrow formation.
The windrow width is adjustable, without the use of tools, from a narrow windrow to a wide, fast-drying swath:
- 91.4 cm (36 in.) up to 216 cm (85 in.) with the roll conditioner
- 114.3 cm (45 in.) up to 216 cm (85 in.) with the impeller conditioner
NOTE: The windrow width depends on the crop conditions and type of conditioner.
Key Specs
Compatibility | 4995, R450, W235, W260 |
Cutting width | 5 m 16 ft |
Cutting height | 1.7-17.8 cm 0.7-7 in. |
Overall width (transport) | 5 m 16.3 ft |
Weight | With fluted steel conditioner 2,371 kg 5,229 lb With urethane conditioner 2,263 kg 4,990 lb With Tri-Lobe conditioner 2,426 kg 5,350 lb |
Windrower
Compatibility | 4995, R450, W235, W260 |
Formation | Adjustable fluffboard and adjustable forming shields |
Impeller conditioner
Width | 2.7 m 8.8 ft |
Diameter | 59.4 cm 23.4 in. |
No. of V-tines | 72 |
No. of speeds | Two-factory setting 624 or 865 rpm Optional 1,000 rpm |
Drive | 4-V powerband belt and sheaves |
Conditioner hood | Adjustable, one lever |
Urethane conditioner rolls
Width | 2.7 m 8.8 ft |
Diameter | 25.4 cm 10 in. |
Material | Urethane |
Surface | Intermeshing, intermittent recessed cleats |
Speed | Platform speed 865 at 2,650 rpm |
Drive | Enclosed gear and shaft drive |
Steel conditioner rolls
Width | 2.7 m 8.8 ft |
Diameter | 25.4 cm 10 in. |
Material | Steel |
Surface | Intermeshing flutes |
Speed | Platform speed 865 at 2,650 rpm |
Drive | Enclosed gear and shaft drive |
Rotary disk cutterbar
Number of disks | 10 |
Reservoir capacity | 9.5 L 12 U.S. qt |
Guard angle | Adjustable; 0-8 degree (angle) |
Dimensions
Cutting width | 5 m 16 ft |
Cutting height | 1.7-17.8 cm 0.7-7 in. |
Overall width (transport) | 5 m 16.3 ft |
Weight | With impeller conditioner 2,135 kg 4,707 lb With fluted steel conditioner 2,371 kg 5,229 lb With urethane conditioner 2,263 kg 4,990 lb With Tri-Lobe conditioner 2,426 kg 5,350 lb |
Windrower width (depending on crop conditions) | With roll conditioner 91-216 cm 36-85 in. With impeller conditioner 114-216 cm 45-85 in. |
Additional information
Date collected |
Accessories and Attachments
FRAME
An adjustable swathboard kit is now available for customers desiring maximum windrow width. This kit will increase windrow width approximately 1-ft. depending on crop conditions.
Windrow width (depending on crop conditions) |
||
|
Without swathboard kit |
With swathboard kit |
With impeller conditioner |
45 in. to 85 in. |
45 in. to 97 in. |
With roll conditioner |
36 in. to 85 in. |
36 in. to 97 in. |
Installation will take approximately 1 to 3 hours.
Miscellaneous
- Replacement Service Side Sheet - BE32536
- Replacement Service Side Sheet - BE32539