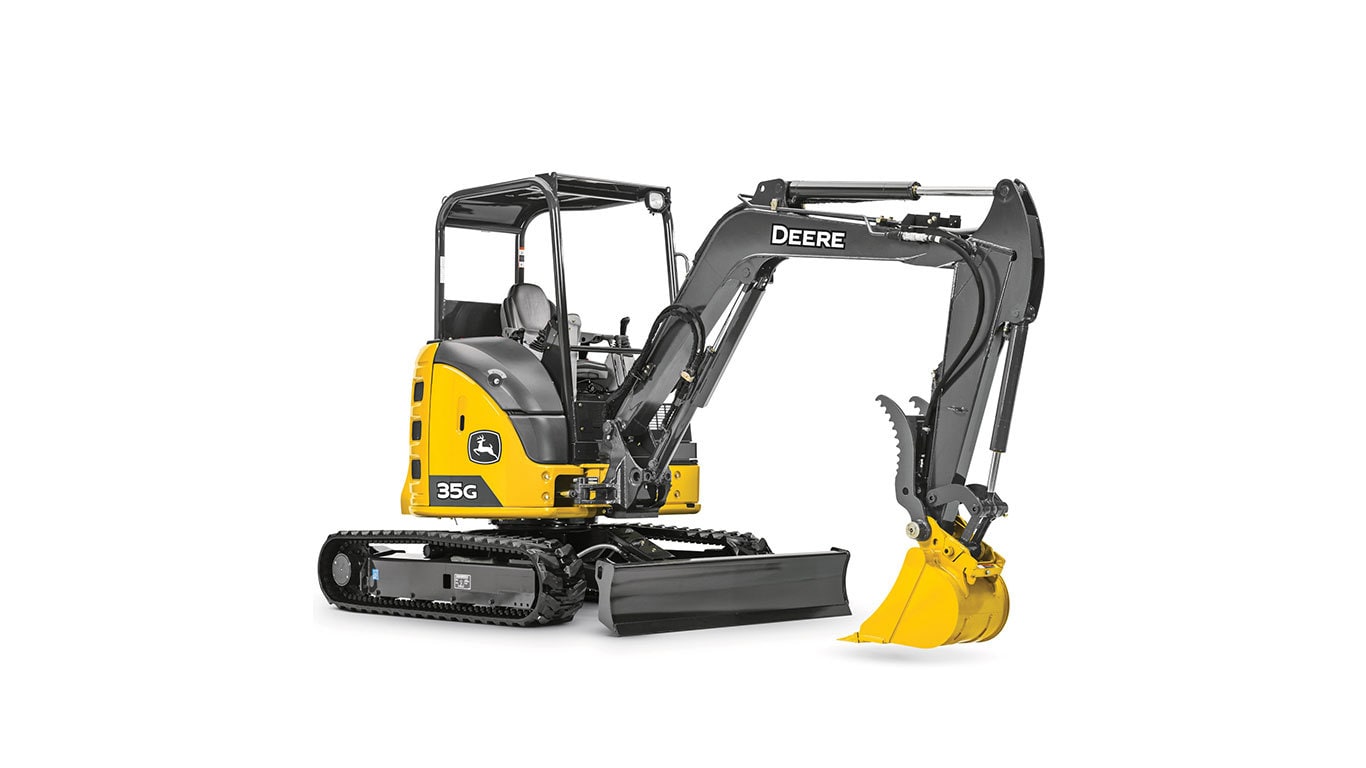
Key Features
- Net Power: 17.4 kW (23.3 hp)
- Max. Digging Depth: 3.06 m (10 ft. 0 in.)
- Operating Weight: 3690 kg (8,135 lb.)
Features
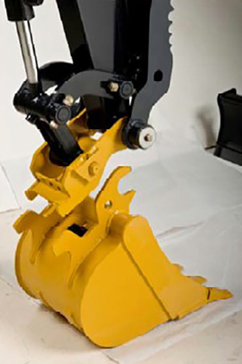
Overview
Think of changing attachments as a system. With the quick connect auxiliary couplers and the manual quick coupler for attachments, changeover to the next attachment is quick with minimal downtime. When using hydraulic attachments, the auxiliary selector valve lets you quickly choose between attachment one-way and two-way flows.
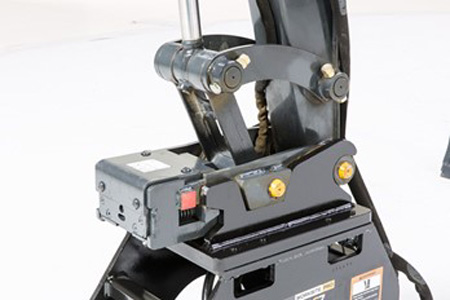
- Hydraulic wedge lock couplers are an additional coupler option available for compact excavators.
- These couplers use wedge lock buckets, thumbs, and adapter plate for attachments.
- These couplers add versatility to underground and landscape customers who frequently change attachments throughout the workday.
Benefits
- All machines have a manual, wear compensating quick coupler that is standard equipment. The wedge design of the locking bar compensates for wear at the joint and keeps the coupler joint tight.
- Mechanical quick coupler makes switching attachments easy with one bolt and two pins.
- Buckets come in a wide range of sizes and two styles: ditch cleaning and heavy duty. They can be changed using the quick coupler system on the unit.
- The clamp, sometimes referred to as a thumb, can be used in conjunction with buckets. This aids in the removal of material if it is bulky and does not fit into the bucket completely.
- Augers feature a self-plumbing bit and reversible rotation for easy withdrawal if an obstruction is encountered
- With the installation of an adaptor plate, all the hammers can be used on John Deere™ Skid Steers, making them a very versatile attachment. John Deere augers can be equipped with numerous sizes of rock, heavy-duty, standard, and tree/shrub bits.
- Hydraulic hammers are perfect for quarry or trench work and concrete removal. Use them to break rock, concrete flatwork, and walls; around rebar; or to a precut line.
Additional Details
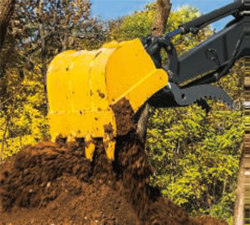
- Compact excavators use common buckets and attachments that customers who own other John Deere compact machines may already have in their fleets
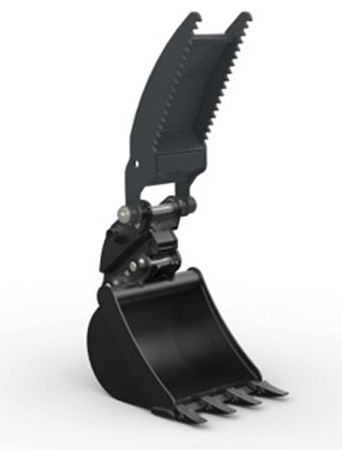
- Pin-Grabber couplers add versatility to underground and landscape customers who frequently change attachments throughout the workday.
- These couplers allow an operator to hook up to the bucket backwards when needed to excavate under obstacles such as sidewalks and utilities.
- Additional buckets, thumbs, and attachment mounting plates are available for use with these couplers.
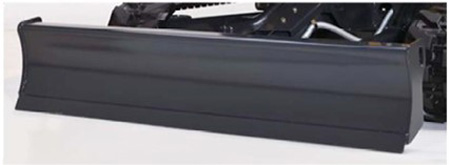
Overview
Make a sizable impact on your productivity and profitability with the backfill blade. The backfill blade can be used to level and backfill trenches. It is the same width as the undercarriage width. The blade can add versatility by using the blade and bucket to clamp and carry pipe, rocks, or other bulky items. A bolt-on cutting edge is available as optional equipment for the backfill blade.
Benefits
- Backfill blade adds versatility, enabling these compact excavators to grade and fill.
- Provides extra stability with attachments or when working on uneven terrain.
Additional Details
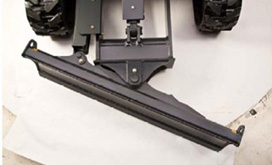
- The optional angle blade decreases backfill time by approximately 20 percent
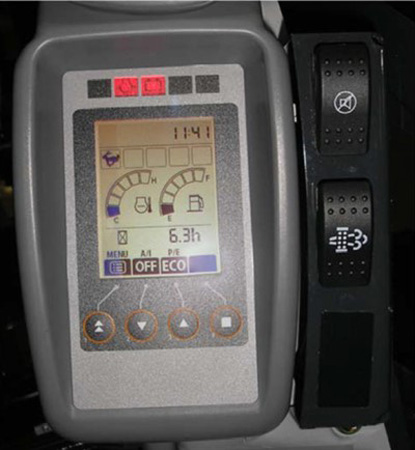
Overview
Low daily operating costs with improved fuel economy and economy/power modes. These machines have improved fuel economy over the previous series.
Benefits
- Auto-idle automatically reduces engine speed when hydraulics aren’t in use.
- Auto shutdown further conserves precious fuel.
- Power/economy modes optimize power for digging applications and significantly improve fuel efficiency.
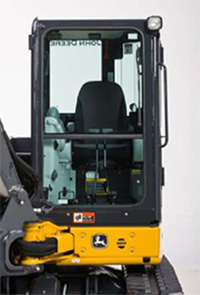
Overview
With large entryways and virtually unrestricted sightlines, the G-Series’ spacious operator stations deliver all the comfort, convenience, and visibility operators need to bring out their best. Their ergonomically designed operator stations are built to accommodate even larger operators.
Benefits
- Spacious operator stations have wide entryways, making entrance and exit easier than ever
- Optional cab’s front glass is expansive, for exceptional visibility and higher productivity
- An adjustable work light at the top left of the canopy or cab increases job efficiency at night
- A slip resistant entry is provided for safe access to the operator’s seat
- Foldable travel pedals increase foot and leg room
- A suspension seat is standard from the factory
- All controls are conveniently located to the operator’s right include the optional radio.
- Pilot control levers enable an operator to control the boom, bucket, arm, and swing functions.
- Automatic, high-velocity bi-level climate-control system with automotive-style adjustable louvers helps keep the glass clear and the operator comfortable
- Control pattern selector valve is conveniently located in a compartment beneath the seat and includes a sight glass that displays the selected pattern
Additional Details
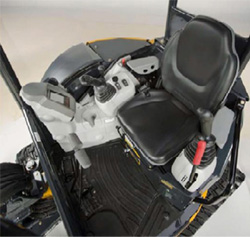
- All canopies and cabs meet the following safety requirements:
- Tip Over Protective Structure (TOPS), Roll Over Protective Structure (ROPS), and Falling Object Protective Structure (FOPS)
- The optional cab comes standard with a heater
- Both the cab and canopy units come with a step area for entry and exit
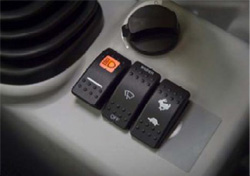
- An auto speed change system for high speed travel is employed.
- The turtle speed lock switch will keep the machine in low when propelling.
- The rabbit speed lock will always keep the unit in the higher mode unless a large load is applied to travel like steering changes.
- The machine will then automatically shift to low but return to high when the load is reduced.
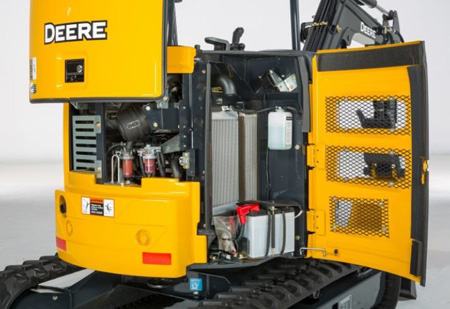
Overview
Extended maintenance intervals enable the machine to remain working for longer periods of productive work before the need to service. This greatly increases uptime and productivity of the unit. Hinged door provides wide-open access to the side-by-side oil cooler and radiator. Cooler design resists trash buildup and allows easier core cleanout. Access is quick and convenient.
Benefits
- Extended oil change and greasing intervals contribute to low daily operating costs.
- Oil impregnated bushings allow the unit to extend grease intervals. Not only does it increase the time between greasing of the unit, this greatly reduces the chances of a problem occurring due to improper maintenance causing downtime to the operation.
- The additional service door allows the operator and technician better access to components during daily service checks and routine maintenance for improved uptime.
- No aftertreatment devices needed reducing maintenance and expense.
- Parts and service are available at over 1,400 John Deere™ dealers throughout North America.
- Wet-disc swing brake provides long-term maintenance-free performance.
Additional Details
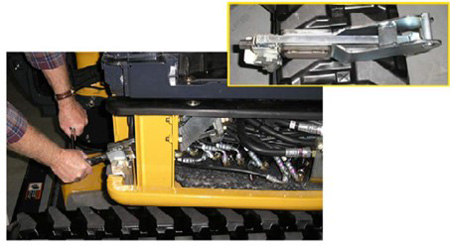
- When maintenance or repair is required, simply use the tilt tool to raise the cab forward to an industry leading 50 degrees. This allows easy access to many components under the floor.
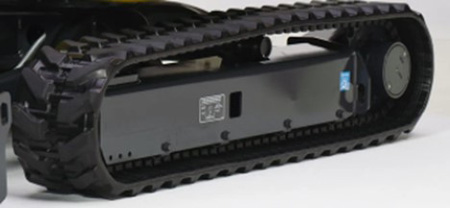
Overview
The X-frame undercarriage is similar to that of larger excavators, and it is designed to shed dirt and debris from the track frames. A track adjuster is located in each track frame and can be adjusted using a standard high pressure grease gun.
Benefits
- Track sag adjustment is conveniently located in the center of the frame to maintain proper track tension and maximize undercarriage life.
Additional Details
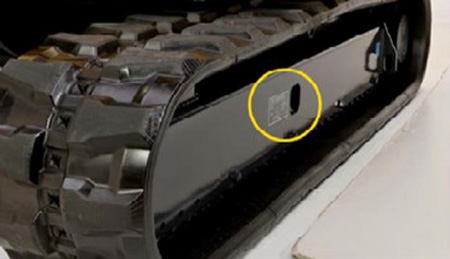
- A track adjuster is located in each track frame and can be adjusted using a standard high pressure grease gun.
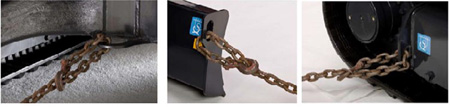
- Tie-downs are provided so loading and transporting of the machine can be done quickly.
- All models have a rear tie down on the rear of the X-frame
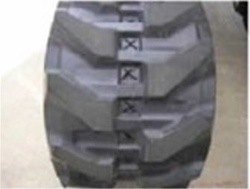
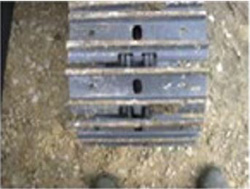
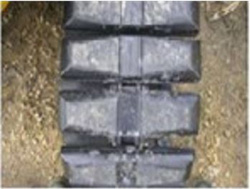
- Rubber tracks are standard equipment.
- Steel track and rubber crawler pads are optional.
DRIVELINE
Emission Rating | Tier 4 |
Engine Manufacturer | Yanmar |
Number Of Cylinders | 3 |
Displacement, ltr (Inches³) | 1.642 (100.2) |
Rated speed, rpm | 2400 |
Engine Output - Net, kW (hp) | 17.4 (23.3) |
Number Of Carrier Rollers - Each Side | 1 |
Number Of Track Rollers - Each Side | 4 |
Track Shoe Width, mm (inches) | 300 (12) |
DIMENSIONS
Transport Length Mono Boom, mm (ft/in) | 4640 (15 ft 3 in) |
Transport Height - Maximum, mm (ft/in) | 2480 (8 ft 2 in) |
Overall Undercarriage Width, mm (ft/in) | 1740 (5 ft 9 in) |
Track Length On Ground, mm (ft/in) | 1660 (5 ft 5 in) |
Overall Undercarriage Length, mm (ft/in) | 2110 (6 ft 11 in) |
Tailswing Radius, mm (ft/in) | 870 (2 ft 10 in) |
Ground Clearance, mm (inches) | 280 (11) |
Dozer Blade Height, mm (inches) | 373 (14.7) |
Dozer Blade Width, mm (ft/in) | 1740 (5 ft 9 in) |
Width over fixed tracks, mm (ft/in) | 1740 (5 ft 9 in) |
Track Gauge, mm (ft/in) | 1440 (4 ft 8 in) |
Digging Reach - Mono Boom, mm (ft/in) | 5210 (17 ft 1 in) |
Dig Height - Mono Boom, mm (ft/in) | 4870 (16 ft ) |
Dump Height - Mono Boom, mm (ft/in) | 3460 (11 ft 4 in) |
Dig Depth - Mono Boom, mm (ft/in) | 3060 (10 ft ) |
Standard Arm, mm (ft/in) | 1315 (4 ft 4 in) |
CAPACITIES
Fuel Tank, ltr (gallons (US)) | 42 (11.1) |
Hydraulic Tank, ltr (gallons (US)) | 32 (8.5) |
Number Of Batteries | 1 |
Voltage, V | 12 |
PERFORMANCE
Ground Bearing Pressure, kPa (PSI) | 32 (4.6) |
Swing Speed, rpm | 9 |
Travel Speed - High, kph (mph) | 4.3 (2.7) |
Arm Tearout, kN (lbf) | 19 (4277) |
Bucket Breakout, kN (lbf) | 27.1 (6085) |
Total Flow, lt/min (gallons (US) / min) | 76.8 (20.2) |
WEIGHTS
Operating Weight, kg (lbs) | 3520 (7760) |